Capabilities
Wyman-Gordon produces high intensity forgings for some of the most technically challenging and demanding applications in the world.
Wyman-Gordon has a long history of providing high-quality pipe products to the energy markets.
Today, it is an internationally-recognized leader in high-end pipe applications and products.
We utilize concurrent engineering techniques with our customers and use both industry standard software and bespoke mathematical modeling to accurately predict the outcome of our forging designs and maximize the forging shape to save material costs.
Through this process modeling, we are able to visualize accurate forging shapes, grain flow, temperature gradients, and strain and structure to ensure the highest quality product to meet our customer specifications and expectations.
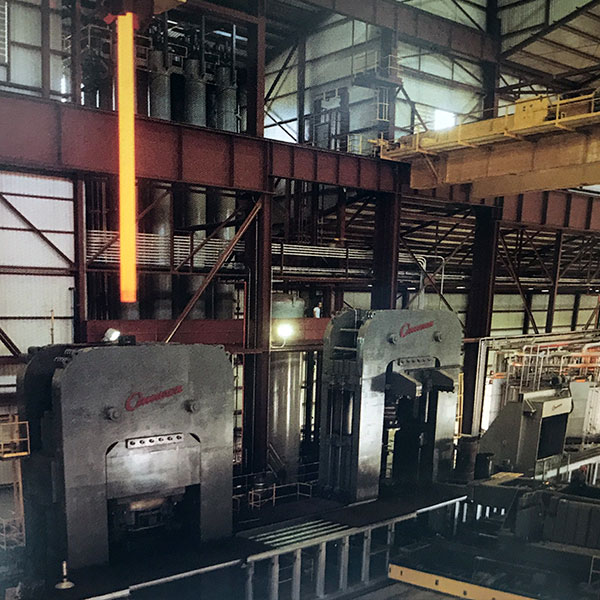
Equipment
Wyman-Gordon produces high intensity forgings for some of the most technically challenging and demanding applications in the world.
- Forge Hammers: 1,000 – 3,000 lbs
- Mechanical Presses: 1,000 – 2,500 Tons
- Screw Press: up to 1,600 Tons
- 2D Matrix Part Making
- Coining Presses: 75 – 750 Tons
- Extrusion Presses: 400 – 440 Tons
- CNC Machines
- White Light Scanner
- Upset & Extrusion Capabilities
- Closed-Die Presses: up to 50,000 Tons
- Ultrasonic Tanks
- Flow Detectors
Materials
Wyman-Gordon manufactures forged components from high grade titanium and nickel based alloys.
Stainless Steel
- 300 & 400 Series
- 17-4-PH
- 15-5-PH
- PH13-8MO
- 21-6-9
Nickel Alloys
- Inconel 600
- Inconel 625
- Inconel 718
- Monel 400
- Monel 500
Aluminum Alloys
- 2014
- 6061
- 7075
Carbon & Alloy Steels
- All Grades
Titanium Alloys
- CP
- 6AL-4V
- 4965
High Temperature Alloys
- Hastelloy*
- Waspaloy**
- A-286
Cobalt-Chrome
- Medical Grade
Zirconium
*Hastelloy is a registered Trademark of Cabot Corp.
**Waspaloy is a registered Trademark of Union Technologies Corp.
Secondary Services
Removal of forging scale by mechanical descaling, wheelabrating and/or chemical cleaning, and passivation.
Nondestructive testing (NDT) operations of magnetic particle inspection (MPI) and fluorescent penetrant inspection (FPI) are performed to the required specifications on heat treated and cleaned forgings. The FPI operation for aircraft parts has been approved by NADCAP-PRI since 1984.
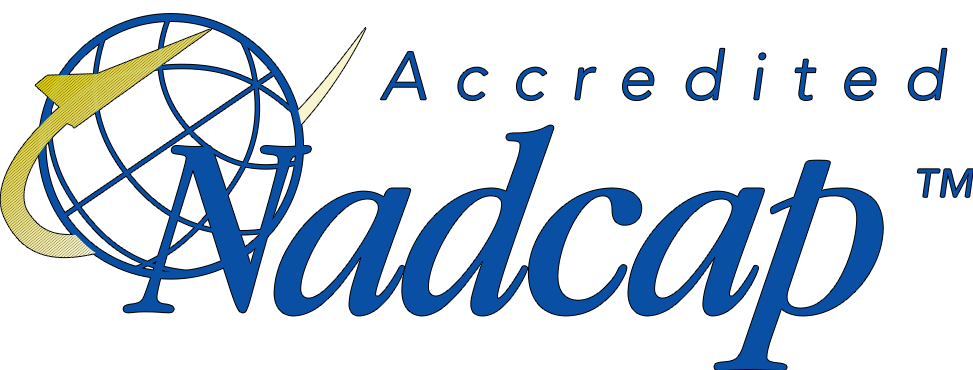